Product Improvement
When a customer already has a product but would like to significantly increase performance, reduce weight, make it faster, increase margin etc., we have always exceeded expectation of our customers. This is because we have extensive experience in design, manufacturing, and simulation. We perform several design/simulation iterations to optimize product design with an understanding that it should be manufacturable at a lower cost.
At Stryker Instruments, they were losing market share on saggital saw which was one of their prime products. Sales dropped from $12 Million to $9 million. Improved performance of Saggital Saw by 80% by redesigning where the company was struggling to improve performance by 3%. Led a team of 40 people and launched product in 6 months which normally takes 2 years. This resulted in the sales increasing from $9 Million to $60 million annually. The motor windings were optimized to improve torque speed curve and manufacturing process was improved to improve the life of the yoke.
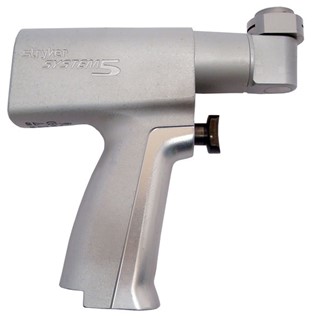
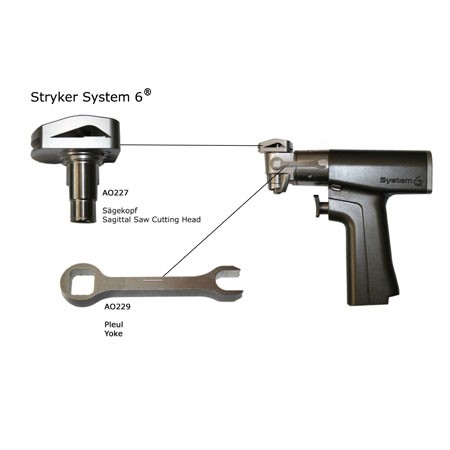
Increased the reliability of Stryker system 6 battery charger by eliminating fan and designing a heat sink that can dissipate all the 4 batteries simultaneously.
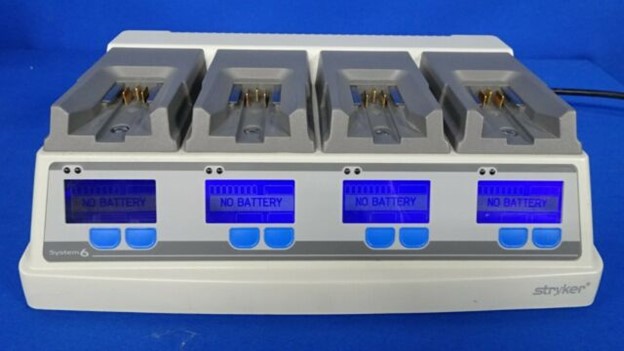
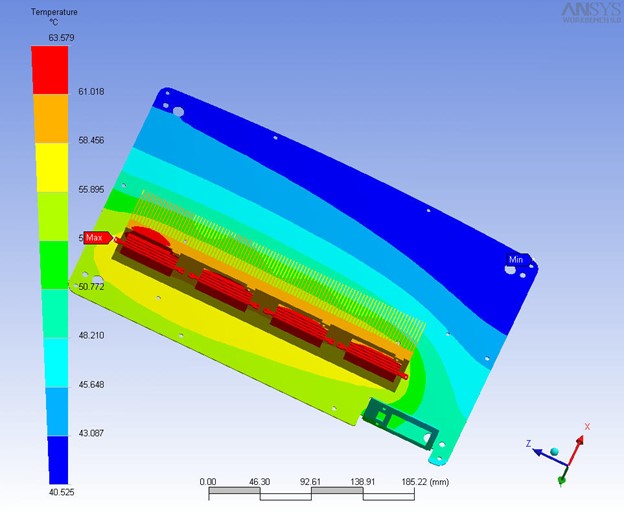
Stryker Dekompressor helps relieve pain caused by contained disc herniations through a procedure called percutaneous discectomy. The titanium screw in the Dekompressor rotates at high speed. This screw failed due to vibration. This failure was due to motor frequency being close to the mode frequency of the titanium screw. We made several changes in design which eliminated failure mode and developed patentable technology which can improve performance by 100%.
Modal vibration was an issue which limited the screw length to 6 inch but surgeons desired it to be 9 inch to treat heavier patient. We were able to build a 9 inch by using simulation and understanding the mode shapes. This ensured that even at 9 inch there was low vibration and no failures.
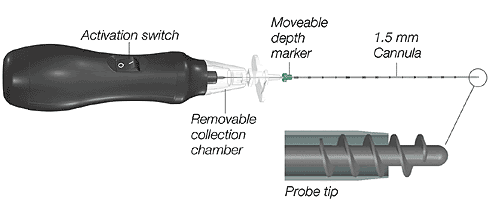
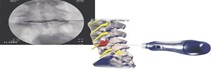
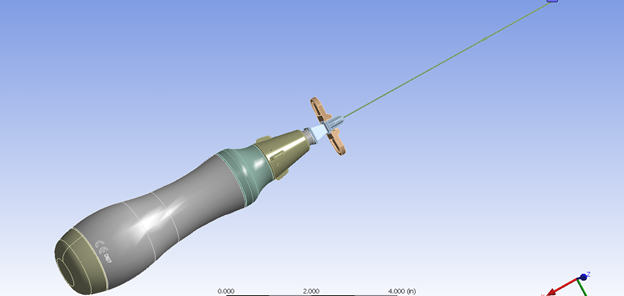
The stryker maestro drill during development had planned to use one engineer and 2 technician to predict wear characteristics inside the drill during a six month period. We helped by performing CFD simulation to see the air pressure and velocity profile to predict wear and we could accomplish the task in 3 weeks what would have taken 6 months.
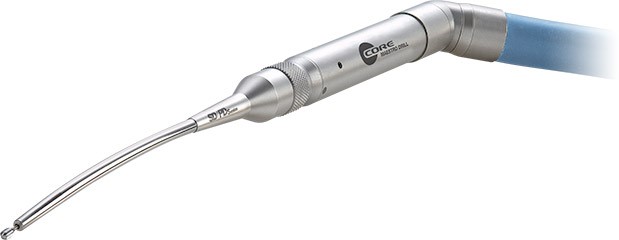
The design was changed to improve the velocity profile.
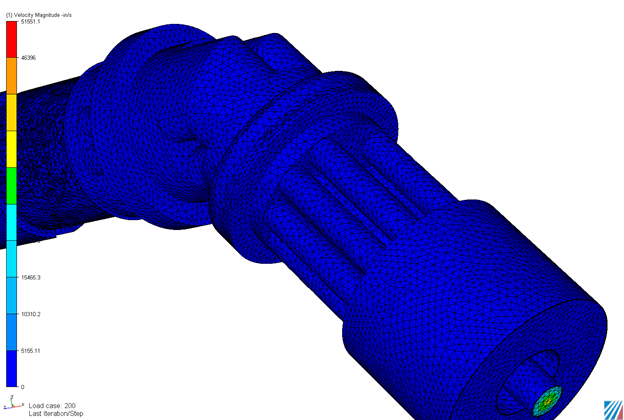
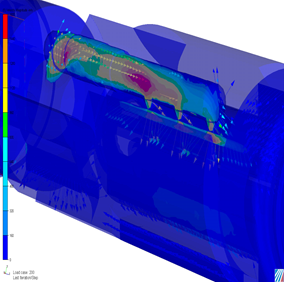
We came up with the concept to convert metallic beds into plastic bed. This would result in cost savings, easy to clean, less parts, significant cost reduction , less shipping cost etc. We led the team to design and perform simulation . The first prototype was success. There are 26 models and the potential savings are $1 Million per model.
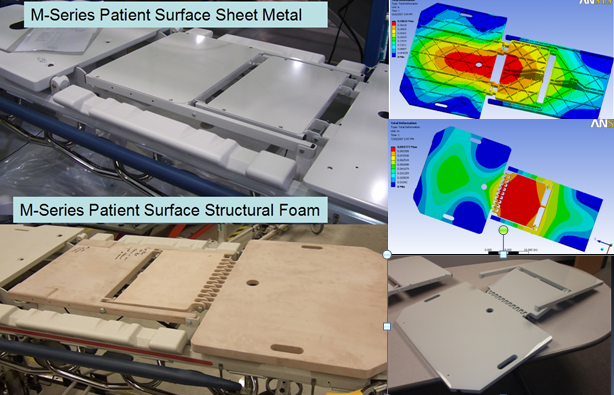
The quality of image deterioted in endoscopes at Stryker after going through autoclave. I ran CFD simulation of the endowscope prism in an autoclave environment and showed that due to thermal stresses the prism moves slightly. We changed material of a part inside the endoscope and we were able to fix the problem resulting in better image after autoclave.
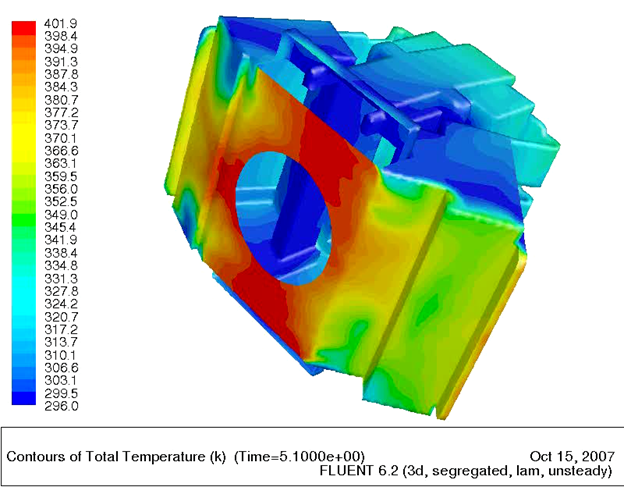