Testing and Simulation
We perform structural, thermal, CFD, Multiphysics simulation to increase reliability, quality, performance and reduce cost. We also help in designing fixtures for testing. We are also able to provide guidance on how to perform data acquisition so that it can be used in simulation to predict realistic results.
Stryker T5 Helmet
Stryker T5 helmet is a product used by surgeons during long surgery to keep their head cool. 90+ percentage customer wanted to return the product because they had headache or blurry vision. We performed simulation and figured out that fan blade frequency was close to the human eyeball frequency resulting in blurry vision and headache. We changed the fan blade material and shape so that its frequency is not close to the eyeball frequency. The problem went away and this saved the $38 million product line.
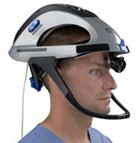
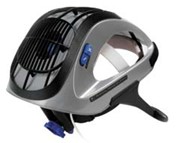
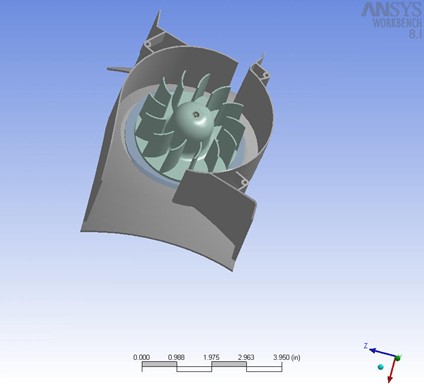
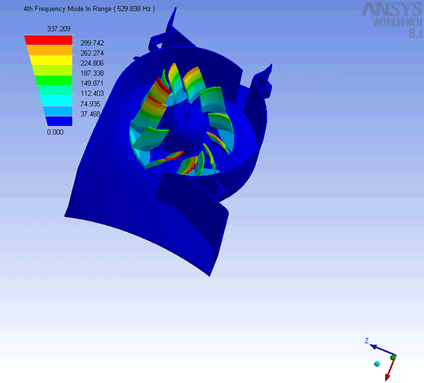
Stryker Robotic Fixture
Stryker performed testing with a robotic fixture, however the test results of product life did not correlate well with the usage in the field. We simulated the forces and stresses while performing testing of saggital saw in the fixture and compared it with hand grip of different people. With the help of simulation we changed the stiffness of the fixture to be close to human hand. The forces calculated in simulation were used later to develop architecture for robotic surgery.
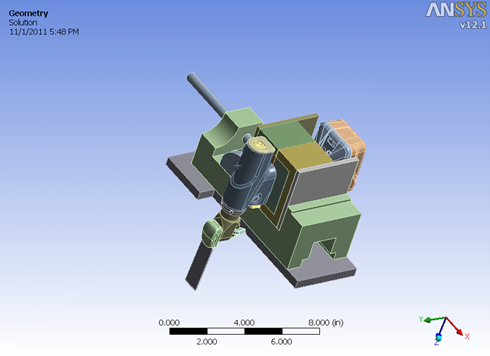
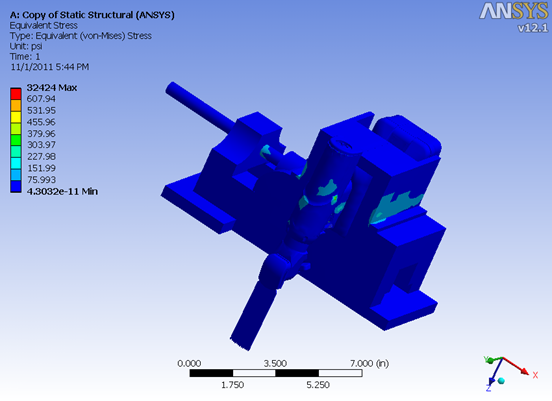
Stryker Maternity Bed
Stryker Medical Maternity bed is a multimillion dollar product line which went on recall due to reduced brake holding force. Stryker could not figure out the reason for several years. We performed simulation and identified the problem in 3 weeks. An aluminum plate had to be changed to steel plate
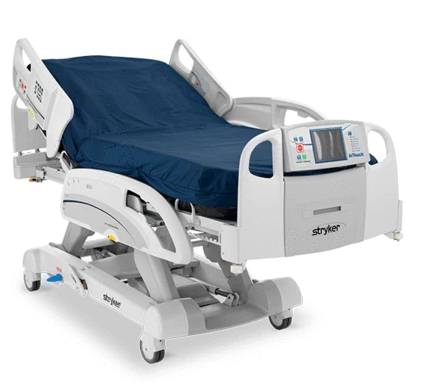
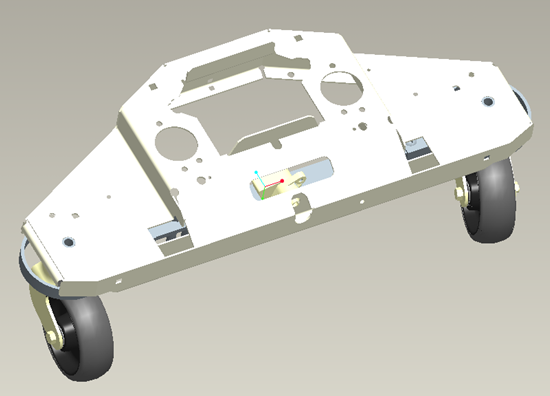

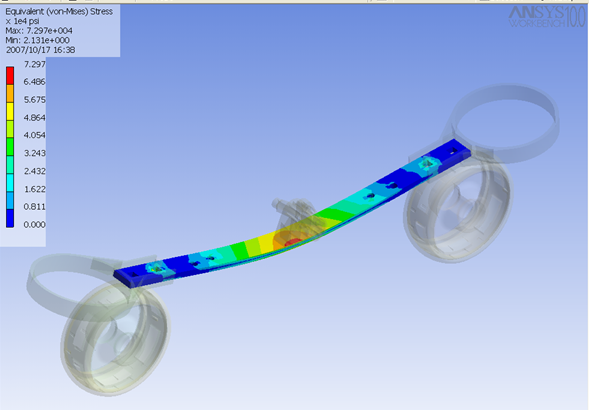
Stryker Bur Chatter Fixture
Designed and developed a Bur Chatter fixture which the Stryker tried and failed for 5 years. This fixture allows Stryker to quantitatively evaluate internal bur design as well as that of competitor. This bur chatter fixture can measure vibration amplitude up to 0.0001 inch for burs running up to 100000 RPM. The design included a setup to move machine in X,Y &Z direction accurately like a CNC machine. We also used pattern recognition and high speed camera (100,000 frames per second) to capture the vibration of the bur while cutting wood.
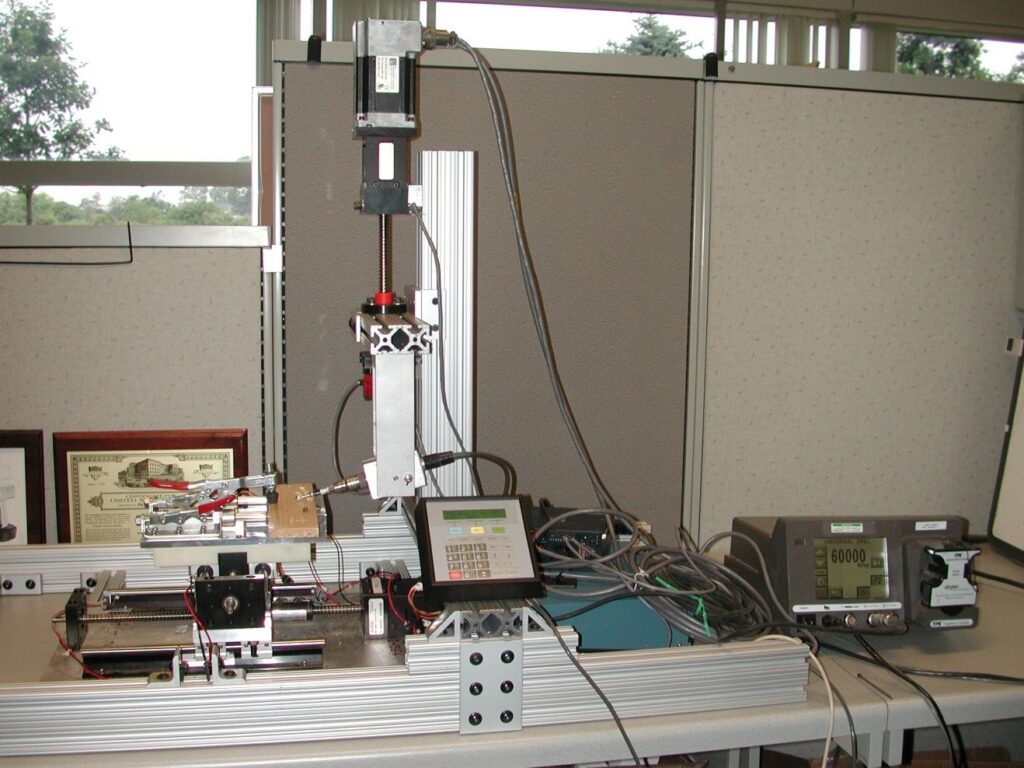
Stryker Medical Bed Crash Simulation
At Stryker, medical bed prototype went through crash testing at 2.6 miles per hour which is an FDA requirement. It took 3 to 4 months to build a prototype and 1-2 months for testing and data analysis. After each testing the design was modified and an updated prototype was built. Each prototype costed $80K and it would take 5 prototypes, 2.5 years and $400K in prototype cost before a new design can pass crash testing. A simulation platform was developed which allowed us to pass crash testing with one prototype in six months saving us 2 years and $320K in prototype cost for launching a new bed. The cost saving in labor was $300K and additional revenue due to early launch resulted in few million dollars per launch. The below video shows the animation of the crash simulation.
Alcon IOL Delivery Simulation
Developed a Simulation platform at Alcon to simulate the delivery of viscoelastic Intraocular lens through delivery systems. You can see the stresses in the lens as it folds and travels through the delivery system. Alcon had tried to develop such a platform with other consulting firms for 10 years and failed. This allowed us to see the failure modes such as shearing and scratching without even making a single prototype of lens or delivery system. This reduced the product development lead time of all IOL by 50%. The Panoptix lens was launched in 2 years instead of 5 years resulting in annual revenue of $50 million.
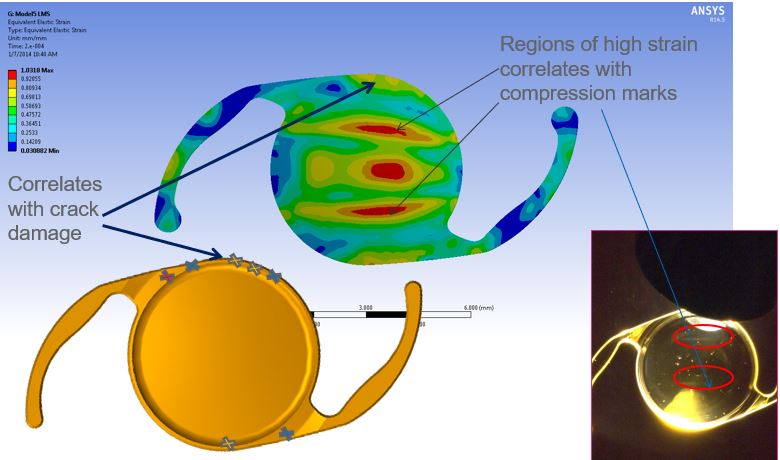